The six-way valve injector is the ideal injector for high-performance liquid chromatography systems. It consists of a circular seal (rotor) and a stationary base (stator). Rheodyne's six-way valve injector is the most versatile instrument used by all major HPLC instrument manufacturers. Working principle: 1. When the handle is in the loading position, the sample is injected into the metering ring through the injection port through the micro injection needle. When the metering ring is full, excess sample is discharged from the emptying hole. 2. Turn the handle to inject (Inject) position, the valve is connected to the liquid phase flow path, the mobile phase is pumped by the pump to wash the loop, and the sample is driven into the liquid phase analytical column for analysis. Although the six-way valve injector has the advantages of simple structure, easy to use, long service life and no daily maintenance, proper use and maintenance will increase the service life, protect the peripheral equipment and increase the analysis accuracy. If properly used, then six-way valve injector can be continuously injected 30000 times without maintenance. The following about the use of six-way valve injector and maintenance matters (for reference): 1, the handle is between Load and Inject, due to temporarily blocked the flow path, the pressure surge in the flow path, and then go Injecting position, high pressure caused damage in the stigma, so the valve should be rotated as soon as possible, can not stay in the middle. Syringe needles used in HPLC systems differ from gas chromatography in that they are flat-head syringes. On the one hand, the outer side of the needle is closely attached to the inner side of the sealing tube of the injector, the sealing performance is good, the liquid is not leaked, no air is introduced, and on the other hand, the needle is prevented from puncturing the sealing component and the stator. 2, six-way valve injector injection method part of the liquid method and the total liquid loading method of two. With a partial liquid injection method, the injection volume can be up to 75% of the loop volume. For example, a 20-g loop can inject up to 15-μL samples and require accurate and identical volumes for each injection. When sampling, the injection volume should be at least 3 to 5 times the volume of the loop, ie a minimum of 60 to 1001aL of sample should be injected into the 20gL loop so that the residual solution in the loop can be completely replaced to achieve the required precision and Reproducibility. Recommended 100ul flat-head syringe with 20ul full-ring injection. 3, according to the needs of the injection volume to produce their own quantitative loop, the general does not require accurate calculation of the quantitative loop volume, for example, a nominal 10gL quantitative loop, the actual 9gL or 1lgL is not important because the measured samples and calibration The injection volume of the sample is consistent, and the errors are offset when calculating the results. 4, sample injection requirements No particles and can stop the needle and injection valve material, the sample solution should be 0.45 ~ tm filter membrane. Prevents particles blocking the injection valve and reduces wear on the injection valve. To prevent buffered salts and other residual material from remaining in the injection system, rinse the injector after each end, usually with a salt-free diluent, water or a salt-free mobile phase. When the injection valve Load Rinse repeatedly with Inject position and wipe the outside of the syringe needle with tissue-free paper.
Angle Light Keel Roll Forming Machine is used with T ceiling, usually used in hotels, railway stations, playgrounds, supermarkets, factories, car transport stations, interior decoration and other places set. It is PLC control, servo tracking cutting, has light weight, high strength advantages.
Specifications:
Raw material
|
PPGI, GI, Aluminum coils
|
Material thickness range
|
0.3-1mm
|
Forming speed
|
30-40m/min(without punching)
|
Rollers
|
12 rows
|
Material of forming rollers
|
45# steel with chromed
|
Shaft diameter and material
|
40mm, material is 40Cr
|
Controlling system
|
PLC
|
Material of cutting blade
|
Cr12 mould steel with quenched treatment
|
Voltage
|
380V/3Phase/50Hz or at your requirement
|
Main motor power
|
4KW
|
Hydraulic atation power
|
3KW
|
Way of driven
|
Gear box
|
Working process:
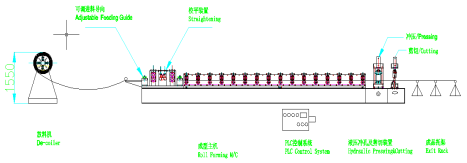
Decoiler - Feeding guide - Straightening - Main roll forming machine - PLC control system - Servo tracking cutting - Receiving table
Pictures of machine:
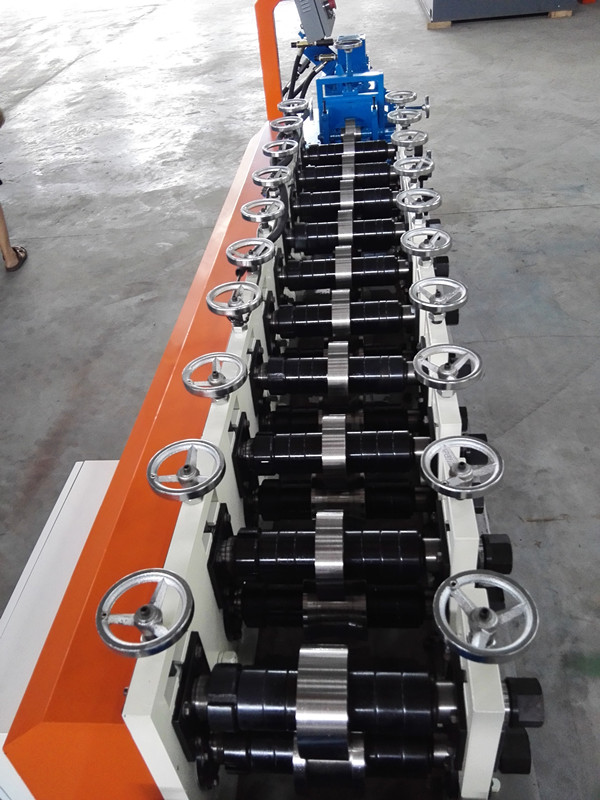
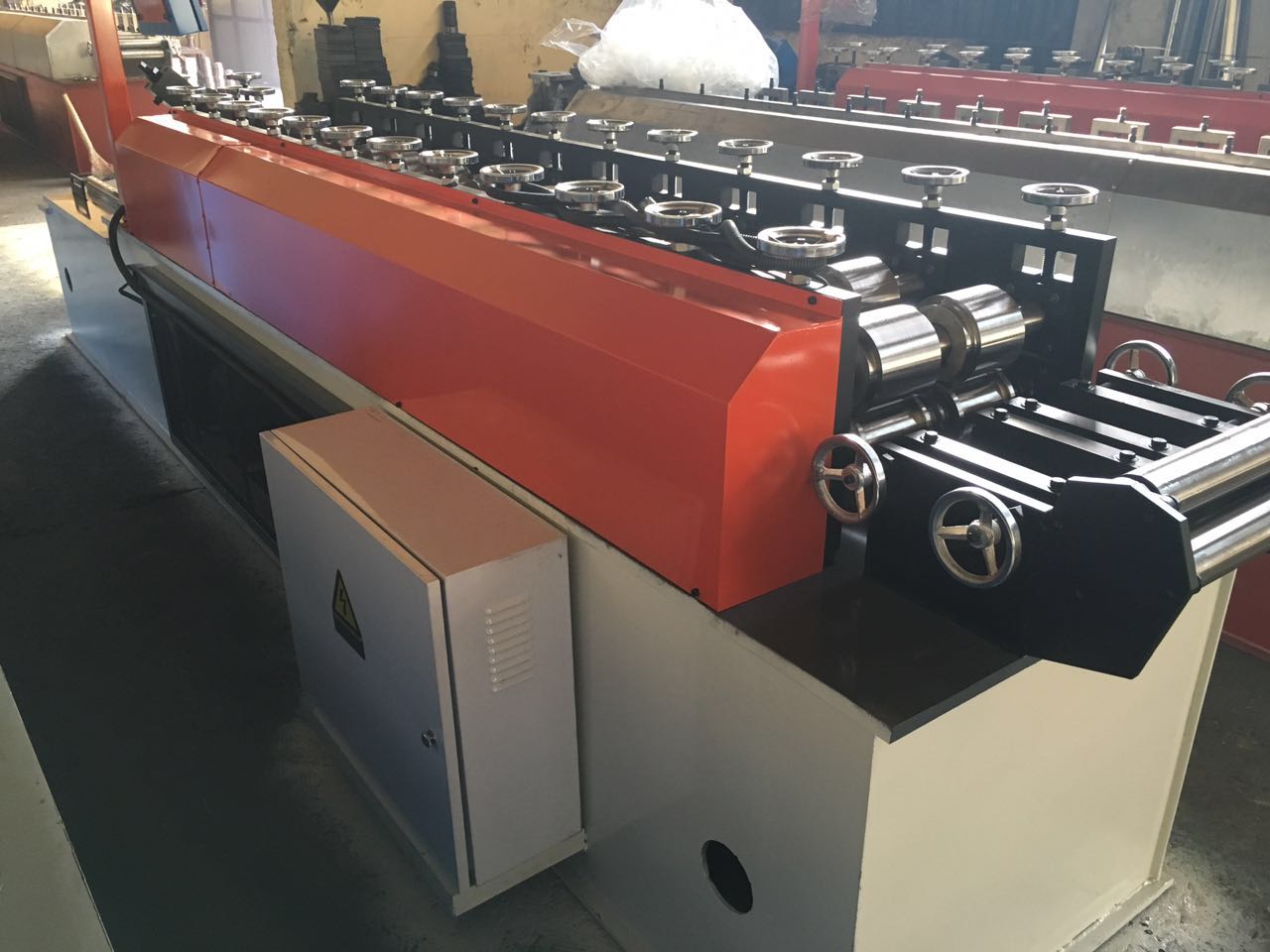
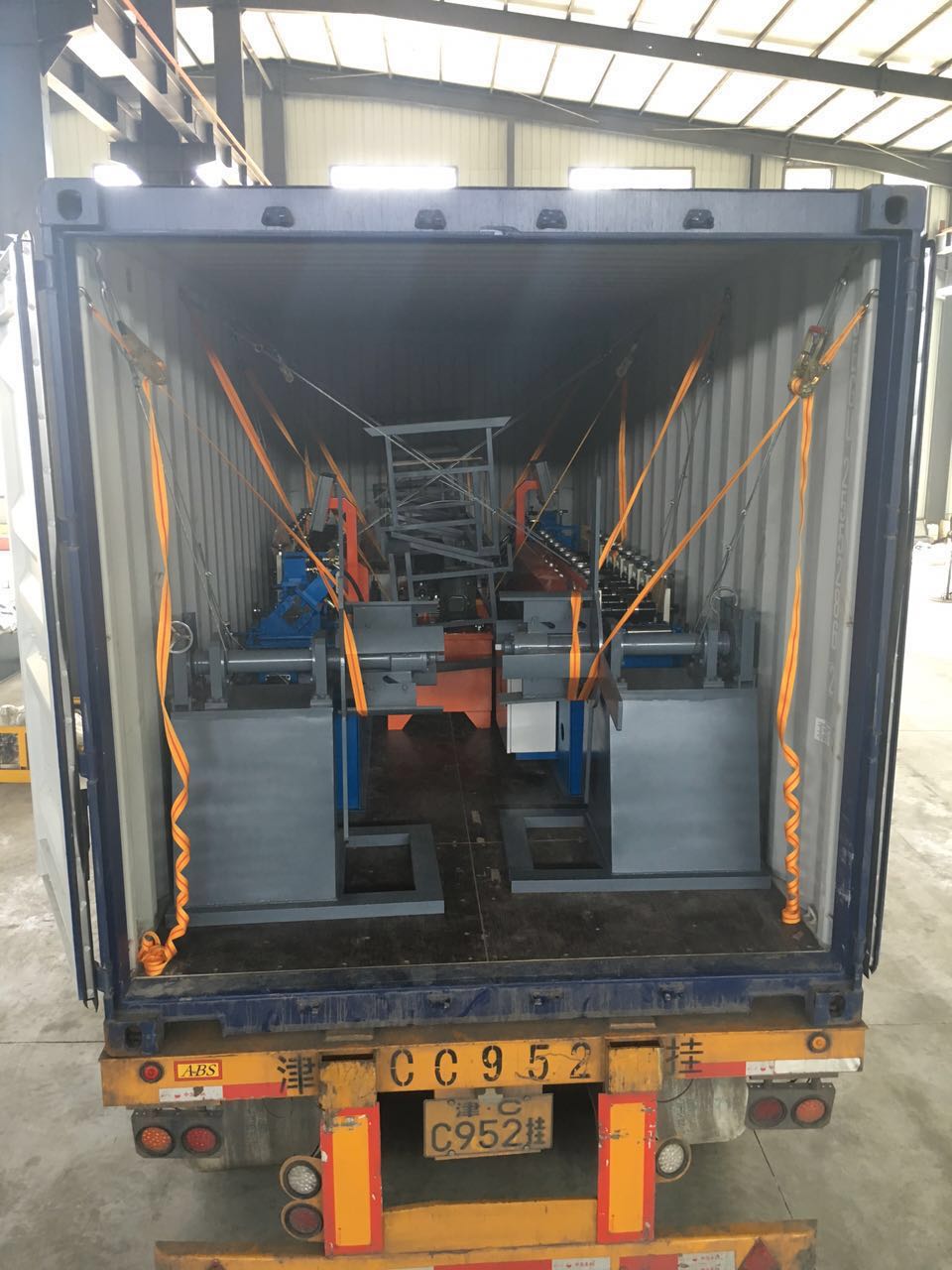
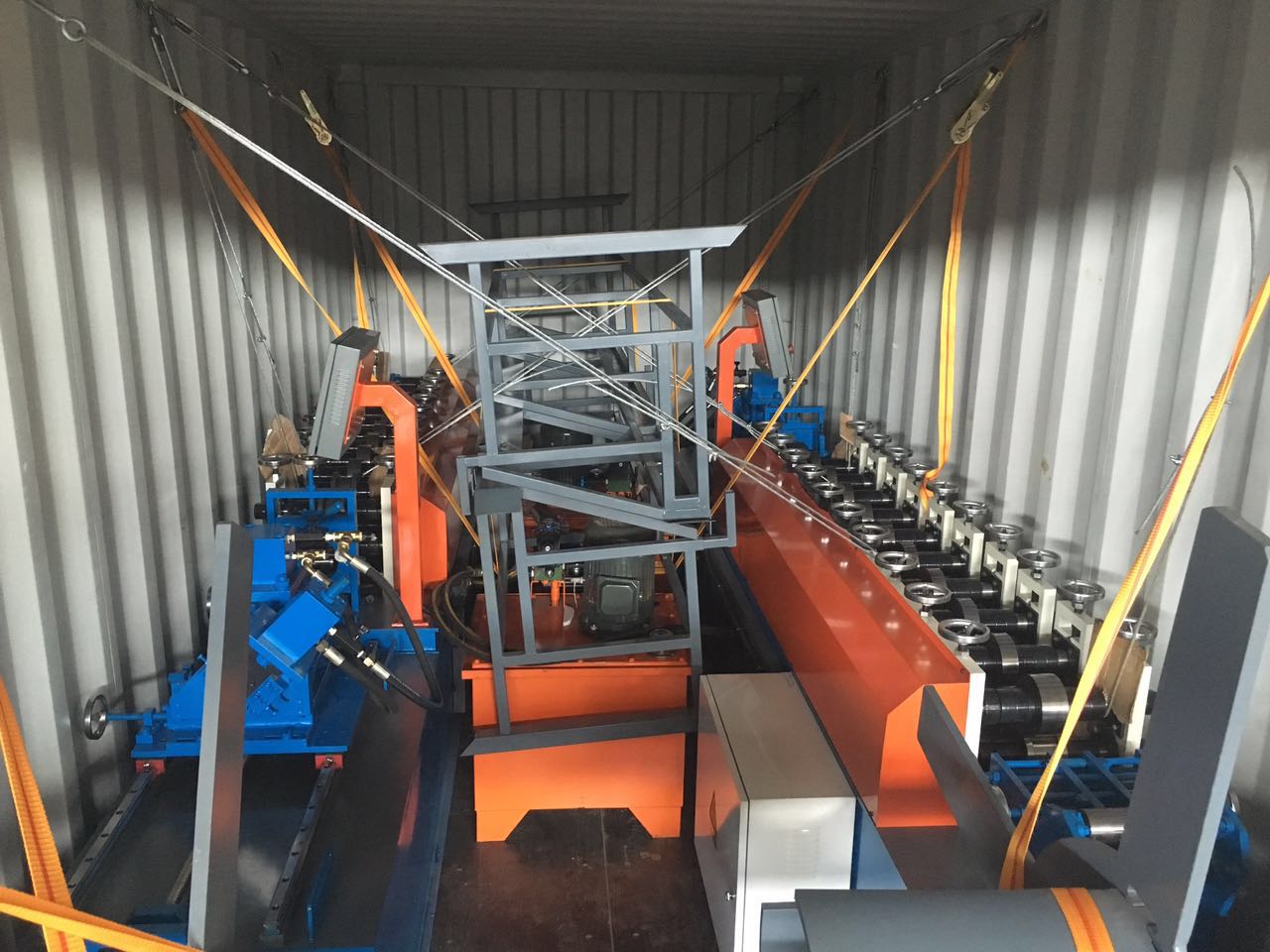
Training and Installation :
1. We offer installation service local in paid, reasonable charge.
2. QT test is welcome and professional.
3. manual and using guide is optional if no visiting and no installation.
Certification and after service:
1. Match the technology standard, ISO producing certification
2. CE certification
3. 12 months warranty since the delivery. Board.
Our advantage:
1. Short delivery period.
2. Effective communication
3. Interface customized.
Angle Keel Forming Machine
Angle Keel Forming Machine,Angle Keel Roll Forming Machine,Steel Angle Keel Roll Forming Machine,Angle Bar Roll Forming Machine
YingYee Machinery and Technology Service Co.,Ltd , https://www.yingyee.cn