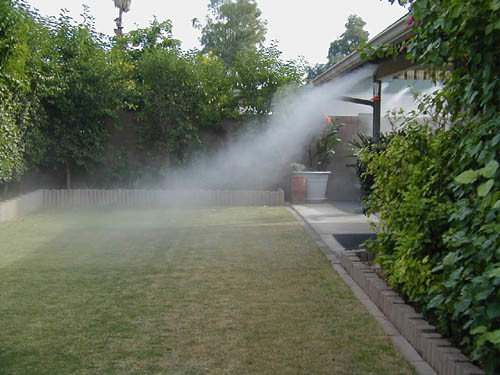
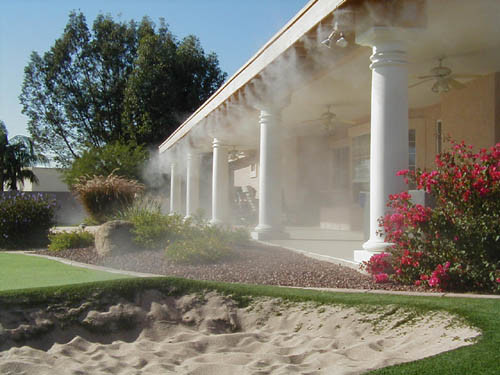
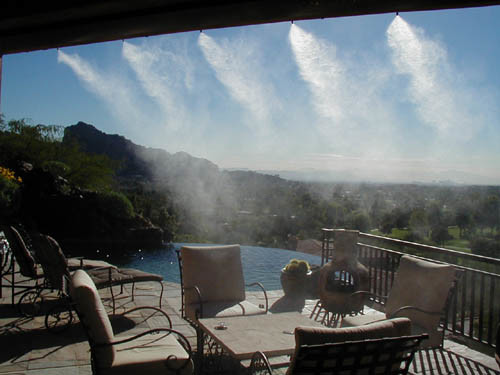
APPLICATIONS OF MISTING SYSTEM AND FOG MACHINE
1. Cooling: Outdoor restaurants play areas, bus stations railway stations, waiting areas, hotels, also for work areas, loading docks, zoos, etc.
2. Suppressing dust: Remove atmosphere dust, recycling, waste and refuse handling, farming, mining, pollution control, decrease unpleasant odor, etc.
3. Increasing humidity: Spinning mills, cotton warehouse, park, greenhouse, testing chambers, flour mills, etc.
4. Agriculture: Poultry farms, mushroom plants, riding arenas, birds and animals, kennels, ensures proper humidity levels and suitable conditions, improves the operations for al kinds of livestock industries.
5. Special effects of mist: Gardens, zoos, malls, fairs, movies sets, water features, fountain, used for creative fog effects.
FEATURES OF MISTING SYSTEM AND FOG MACHINE
W108-04N can connect 5 high pressure nozzles installed on a copper ring
W108-13N can connect 13 high pressure nozzles
W108-45N can connect 45 high pressure nozzles
Stainless steel housing
Fog can spray with different frequencies controllered by the Timer
The Pump will stop working automatically when lack of water
MODEL NO. | FLOW RATE | PRESSURE | RPM | POWER | DIMENSION | G. W. | |
W108-05N | 0.3L/MIN | 60BAR, 870PSI | 1400R/MIN | 120W | 40*20*27CM | 8.5KGS | |
W108-10NS | 0.5L/MIN | 40Bar, 580PSI | 1200R/MIN | 120W | 38*18*45CM | 9KGS | |
W108-10NR | 0.5L/MIN | 40Bar, 580PSI | 1200R/MIN | 120W | 45*25*28CM | 9KGS | |
W108-13N | 1L/MIN | 80BAR, 1150PSI | 1400R/MIN | 200W | 43*22*29CM | 11KGS | |
W108-45N | 3L/MIN | 60BAR, 870PSI | 1400R/MIN | 800W | 47*25*32CM | 18KGS |
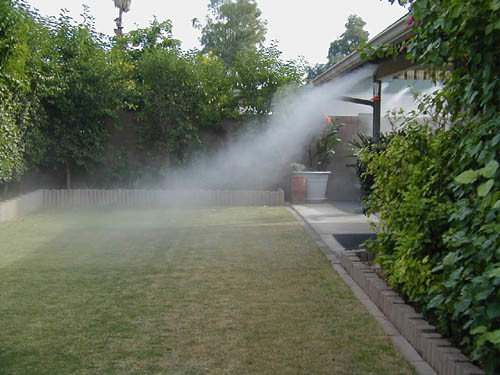
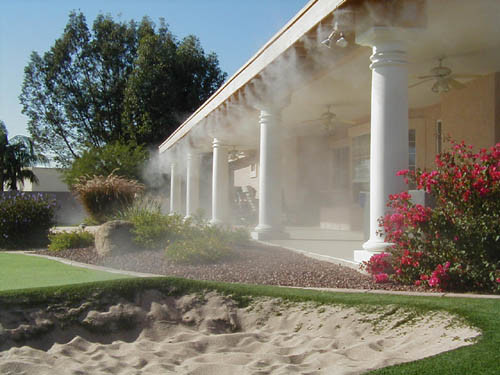
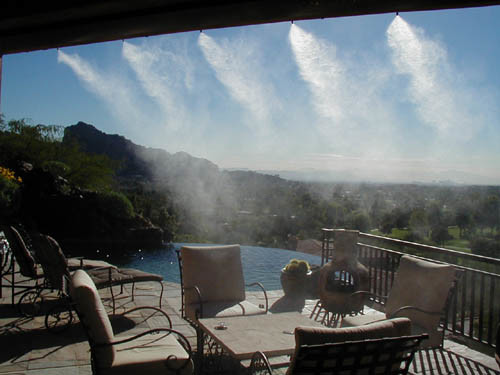
APPLICATIONS OF MISTING SYSTEM AND FOG MACHINE
1. Cooling: Outdoor restaurants play areas, bus stations railway stations, waiting areas, hotels, also for work areas, loading docks, zoos, etc.
2. Suppressing dust: Remove atmosphere dust, recycling, waste and refuse handling, farming, mining, pollution control, decrease unpleasant odor, etc.
3. Increasing humidity: Spinning mills, cotton warehouse, park, greenhouse, testing chambers, flour mills, etc.
4. Agriculture: Poultry farms, mushroom plants, riding arenas, birds and animals, kennels, ensures proper humidity levels and suitable conditions, improves the operations for al kinds of livestock industries.
5. Special effects of mist: Gardens, zoos, malls, fairs, movies sets, water features, fountain, used for creative fog effects.
FEATURES OF MISTING SYSTEM AND FOG MACHINE
W108-04N can connect 5 high pressure nozzles installed on a copper ring
W108-13N can connect 13 high pressure nozzles
W108-45N can connect 45 high pressure nozzles
Stainless steel housing
Fog can spray with different frequencies controllered by the Timer
The Pump will stop working automatically when lack of water
MODEL NO. | FLOW RATE | PRESSURE | RPM | POWER | DIMENSION | G. W. | |
W108-05N | 0.3L/MIN | 60BAR, 870PSI | 1400R/MIN | 120W | 40*20*27CM | 8.5KGS | |
W108-10NS | 0.5L/MIN | 40Bar, 580PSI | 1200R/MIN | 120W | 38*18*45CM | 9KGS | |
W108-10NR | 0.5L/MIN | 40Bar, 580PSI | 1200R/MIN | 120W | 45*25*28CM | 9KGS | |
W108-13N | 1L/MIN | 80BAR, 1150PSI | 1400R/MIN | 200W | 43*22*29CM | 11KGS | |
W108-45N | 3L/MIN | 60BAR, 870PSI | 1400R/MIN | 800W | 47*25*32CM | 18KGS |
"Gravity Die Casting. A permanent mould casting process, where the molten metal is poured from a vessle of ladle into the mould, and cavity fills with no force other than gravity, in a similar manner to the production of sand castings, although filling cn be controlled by tilting the die."
Gravity Die Casting
Sometimes referred to as Permanent Mould, GDC is a repeatable casting process used for non-ferrous alloy parts, typically aluminium, Zinc and Copper Base alloys.
The process differs from HPDC in that Gravity- rather than high pressure- is used to fill the mould with the liquid alloy.
GDC is suited to medium to high volumes products and typically parts are of a heavier sections than HPDC, but thinner sections than sand casting.
There are three key stages in the process.
- The heated mould [Die or Tool] is coated with a die release agent. The release agent spray also has a secondary function in that it aids cooling of the mould face after the previous part has been removed from the die.
- Molten metal is poured into channels in the tool to allow the material to fill all the extremities of the mould cavity. The metal is either hand poured using steel ladles or dosed using mechanical methods. Typically, there is a mould [down sprue" that allows the alloy to enter the mould cavity from the lower part of the die, reducing the formation of turbulence and subsequent porosity and inclusions in the finished part.
- Once the part has cooled sufficiently, the die is opened, either manually or utilising mechanical methods.
Advantages
- Good dimensional accuracy
- Smoother cast surface finish than sand casting
- Improved mechanical properties compared to sand casting
- Thinner walls can be cast compared to sand casting
- Reverse draft internal pockets and forms can be cast in using preformed sand core inserts
- Steel pins and inserts can be cast in to the part
- Faster production times compared to other processes.
- Once the tolling is proven, the product quality is very repeatable.
- Outsourced Tooling setup costs can be lower than sand casting.
Gravity Casting Parts,Aluminum Alloy Gravity Casting Parts,Aluminum Gravity Die Casting Parts,Gravity Casting Aluminum Parts
HSI INDUSTRIEL LTD , https://www.hsiindustriel.com