Model NO.: GXC1000
Certification: CE
Structure: Top Feeding, or Side Feeding
Trademark: Genox
Transport Package: Film with Wooden Pallet
Specification: as requirement
Origin: Guangzhou
HS Code: 8477800000
Gran-Excalibur (GXC Series) Heavy Duty Granulators are designed for high throughput size reduction of larger sized products in a single pass. These machines are also ideal for secondary granulation when positioned behind pre-shredders in various types of recycling systems. Incorporating various different methods of wear protection such as replaceable wear plates and resistant surface coatings, the GXC machines are well suited to processing abrasive, contaminated materials such as glass filled plastics and dirty films containing sands.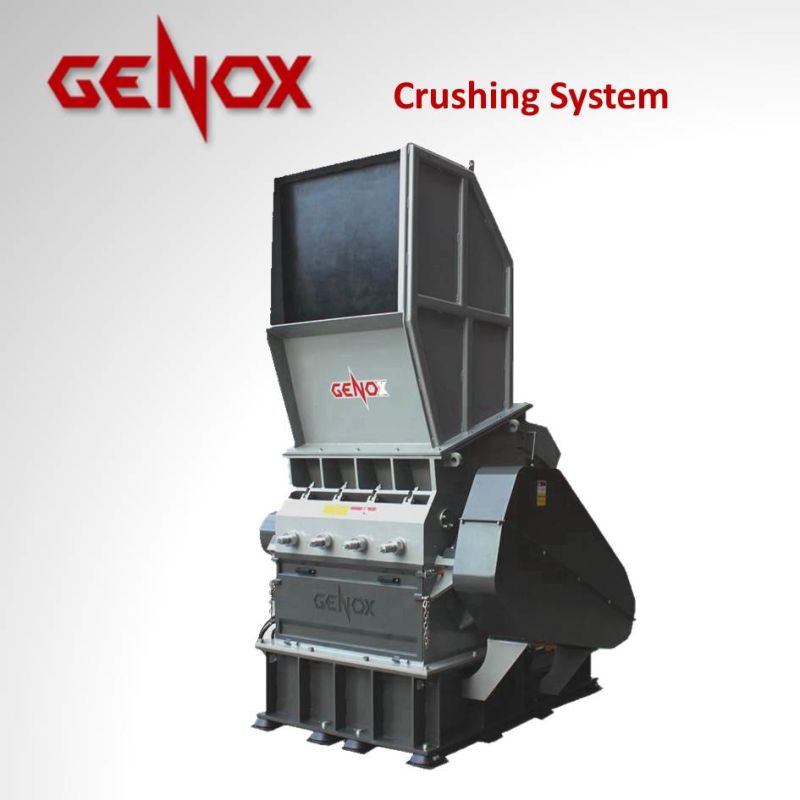
Standard Features
· Strong welded construction from heavy gauge steel plate
· Inclined, split cutting chamber design
· Oversized, outboard spherical rotor bearings prevents bearing damage due to product migration
· Precision machined rotors (Forward set V-Rotor as standard)
· Manual, electric and hydraulic chamber opening mechanisms - quick access to the cutting chamber for maintenance and machine clean downs
· Replaceable wear plates at either end of the rotor shaft
· Stand Alone Electrical Control Panel - using quality Schneider (Telemecanique) components and Siemens PLC's
· Tested, Approved and Certified to the applicable CE safety standards
GXC Series Rotor Configurations
As standard, GXC series machines are supplied with our open V-Rotor as standard which is suitable for most types of material. The double shear, V configuration of the forward set blades creates a highly efficient double scissor cut, and encourages material to the centre of the cutting chamber. This results in reduces power consumption, even blade wear, reduced wear on the chamber sidewalls and optimum throughput. The open design of the rotor lets material expand and move around and allows good airflow through the machine. This minimizes heat build up and production of fines. Granulators can be supplied with 3, 5, 7 or 9 rows of rotor blades depending on the model. A rear set V-rotor design (known as the VS-Rotor) is also available for certain, lighter duty applications.
The C-Rotor is a heavy duty, high inertia, semi-closed design intended for demanding applications. The larger quantity of individual blades are held by strong supporting segments and can be replaced piece by piece if required. This design creates a cascade cutting effect which is well suited for processing hard or thick materials and is also a popular choice when granulating profiles. The C-rotor is available with 3, 5 or 7 staggered rows of blades depending on the model.
Â
model | GXC1000 |
Dimension L X W X H(mm) | 2120×2010×3700 |
Hopper opening W X H(mm) | 1000×1000 |
Rotation diameter(mm) | Ø 520 |
Rotor operation length(mm) | 1000 |
Rotation speed(rpm) | 520 |
Standard screen (mm) | Φ12 |
Rotor knives (pcs) | 5×2 |
Counter knives (pcs) | 2×1 |
Drive power (kW) | 55~90 |
Hydraulic power (kW) | 1.5 |
Weight (kg) | Approx 4800 |
Alloy Steel
Alloy steels are iron-based materials that contain one or more alloying element to create specific properties. One of the most common examples is 4130 Alloy Steel, which contains molybdenum as well as chromium and is hardenable by heat treatment. Please visit the alloy steel forgings page to learn about other alloy steel grades.
Forged Alloy Steel,Forging 4130,Forging 4340,Forging 4340
Jinan Paiwo Engineering Machinery Co.,Ltd , https://www.paiwoforging.com